
Material Guide: ACM Rubber
Our Guide To ACM – Acrylic Rubber
Polyacrylic rubber, also known as ACM, are manufactured elastomers that are created from acrylic monomers. ACM is created through a process of emulsion or suspension polymerisation, which is designed to make these moulded rubber components suitable for use in the most testing environments.

What Are The Advantages Of ACM Rubber?
It has an array of properties that make it suitable for use in a range of hard-wearing applications. The key feature of ACM is its incredibly high resistance to hot hydraulic oil and oxidation, making it ideal for use in hydraulic machinery and equipment. Furthermore, ACM is naturally resistant to ozone and weathering, which makes it far superior to nitrile rubber (NBR).
What Are The Disadvantages Of ACM Rubber?
Despite ACM being well suited to a range of applications, particularly environments that face weathering and environmental pressures, this rubber will not be well suited to environments that face large amounts of water and rain damage. This is due to ACM having poor water resistance, as well as low resistance to low temperatures. This moulded rubber solution is only suitable in applications as low as -10°C. Also, ACM has a poor level of resistance to acids and alkalis.
Additionally, ACM does have a very low resilience in temperatures below 70°C. However, despite this, it has found use in vibration damping.
What Are The Typical Applications Of ACM?
Typical applications for ACM include:
- Automotive Components
- Textiles
- Adhesives
- Coatings
What Temperatures Does ACM Suit?
ACM has a typical working temperature range from -10°C to 150°C.
Looking for more detailed information on the different types of rubbers and polymers we work with? Then check out our material guides where you can find FAQ’s and more guides like this one detailing all you need to know. If you are looking for rubber or polymer products get in touch with DLR Elastomer today via our contact page or via LinkedIn and we can chat over your requirements.
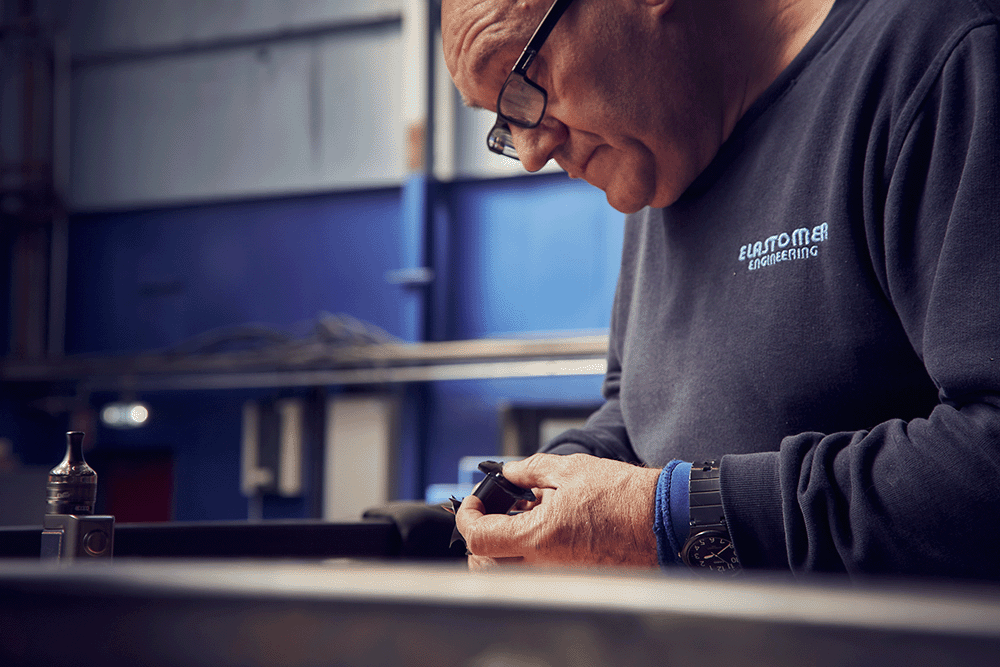
Any questions? Get in touch
Since 1895 DLR has been combining expansive knowledge of materials, their properties, and processing techniques to develop bespoke mouldings and fabrications for many industry sectors. Our core services include moulding rubber, rubber sheeting, Petroseals, and cast polyurethane products. If you have any questions about our products, our process or the materials we use get in touch today!