
Our Rubber Process
At DLR, we work in close collaboration with clients to understand their needs. We support all stages of your project, from initial design & material selection, through to prototype testing, manufacturing & production.


Design
Informed by decades of experience in materials technology, our polymer design engineers generate effective and efficient solutions. We utilise the best available rubber design tools for rubber moulding.
Development
When it comes to the rubber development stage, DLR aims to imprint their engineering and materials science knowledge and expertise on every rubber production solution. The end goal is to present the client with a component that matches the client’s exact demands.


Manufacturer
With the design and development processes cleared, the last stage is our rubber manufacturing process. Through many years of research and development, our design processes have been streamlined to result in the successful and economical rubber manufacturing services for which we are well known.
Design Process
Informed by decades of experience in materials technology, our polymer design engineers generate effective and efficient solutions. We utilise the best available rubber design tools for rubber moulding and have acquired the Baulé computer-controlled mixing and dispensing machine, enabling us to extend our range of polyurethane materials. Our rubber moulding and casting design projects are also aided by FEA modelling and 3D CAD software.
Rubber sheeting supports applications in many industry sectors. Sheet rubber requires excellent protection properties to work effectively within hazardous environments where exposure to chemicals, weathering and abrasion are commonplace. Due to its flexibility and elasticity at high and sub-zero temperatures, rubber sheeting is typically used as horsebox matting, pond lining, roof covering, fire retardant and as a gas & chemical barrier in food and medical applications.
This helps us to understand the needs of your application thoroughly. We’re also happy to share our polymer design knowledge and how DLR products form essential parts of specialised equipment. If you have any further questions regarding our design process, check out our FAQ section below.

Development Process
When it comes to the rubber development stage, DLR aims to imprint their engineering and materials science knowledge and expertise on every rubber production solution. The end goal is to present the client with a component that matches the client’s exact demands, however challenging they might be. Our ‘Design to Manufacture’ concept ensures we can source, fabricate and produce parts that not only meet your requirements but exceed them.
Materials science, tooling and process technology come together during the rubber development stage to produce the component. Modifications to the materials, tooling and process can now be made to optimise all elements of the made-up part.
These sample products are then tested by DLR and the clients, who can do so in the application itself, to ensure their functional requirements are met. This iterative process ensures client satisfaction with all of our rubber production projects, whether it is rubber moulding or polyurethane casting.

Manufacturing Process
With the design and development processes cleared, the last stage is our rubber manufacturing process. Through many years of research and development, our design processes have been streamlined to result in the successful and economical rubber manufacturing services for which we are well known.
Our range of presses provides flexibility, enabling us to choose the most appropriate method of curing from injection, transfer, compression moulding and rotocuring.
In order to evaluate performance and ensure successful trials to verify the design, DLR can quickly and easily produce parts for clients. For more information on our rubber manufacturing process, view our FAQs below.
Our Process FAQ
Yes, plastics are polymers. Rubbers, elastomers are polymers. Plastics and rubbers are two different sets of polymers.
A polymer is a material with a long chain molecular structure, rather like spaghetti. These long chains are formed in reactors that polymerise or put together small units called monomers.
Polymers can be divided into two main groups – thermoplastics and thermosets. Thermosets are rubbers often used to make tyres, shoe soles and car door seals, just to name a few applications.
Thermoplastics are divided into two categories – semi-crystalline and amorphous. In general, amorphous polymers will scatter light and can be water clear. Depending on the polymer design, crystalline polymers can be translucent or opaque and find use in many household goods.
TPE, TPV and TPR are materials with elastic properties. These have a rubbery feel, and like all thermoplastics, can be recycled, reused and reformed into other products.
Yes! All rubbers and elastic materials are available in a range of colours. Depending on the application, we can recommend specific polymers that will retain their colour in service. Some polymers may discolour and fade under the influence of UV and artificial light.
Carbon black is black in colour and widely used as a reinforcing filler. This type of polymer design is cost-effective and efficient, providing the correct balance of physical properties required for any given application.
Non-black mineral fillers such as silicates, silicas, clays and calcium carbonates can produce different coloured rubbers. Our rubber design tools enable us to compound and produce non-black rubber parts.
The hardness of a rubber product defines its physical properties and its application to a large extent. It is the most fundamental property, along with density and specific gravity. Polymer hardness defines how much the rubber can be deformed without being damaged. In technical terms hardness is a synonym for modulus, the stress at a given strain – this defines the stiffness of the material.
High hardness equates to a stiffer material, low flexibility, and a higher tensile strength that is more resistant to abrasion. Conversely, lower hardness or softer materials equate to a less rigid (or low modulus) material. This can give your polymer design greater low-temperature flexibility, high tensile strength and abrasion resistance.
As a general rule, a lower density indicates a rubber rich compound, meaning better quality. Higher densities are typically achieved by adding low-cost fillers.
In short, the answer is yes. There are a few techniques that rubber moulding companies employ.
A suitable rubber solution, usually solvent based, can be used to coat rubber onto metals. The polymer design is dipped and then vulcanised. Depending on the amount of rubber required, an over moulding may offer a better solution.
On metal parts, rubber can act as a barrier to heat and chemicals. Rubber insulates and offers a warmer surface to hold onto and provide grip or friction for leverage.
Rubber can be used in applications that cover a temperature range of 380°C. This covers use at temperatures as low as -80°C and up to 300°C! Some parts can be used at elevated temperatures and in the presence of gases, liquids and solids.
Exposing rubber parts to aggressive environments, in combination with high temperatures, presents its own challenges. The vast majority of rubber applications are well below the 150°C mark. Most are at ambient temperatures, with regular exposure to the elements, e.g. car tyres and car door seals.
Industrial and domestic applications are generally indoors and exposed to various corrosive and non-corrosive media. Typical rubber injection moulding applications include washing machine door seals, rollers in printers and copiers, and parts in water fittings such as domestic heating and bath fittings.
Natural rubber has the potential to be very environmentally friendly. However, the vulcanisation reaction means it has difficulty biodegrading. Synthetic elastomer manufacturers have been producing methane from sugar cane alcohol to reduce their reliance on crude oil and huge refining installations. The methane is then polymerised to produce the polymers, which are made into the rubber products we know and use.
These polymers are costly to manufacture, but production costs are likely to come down as synthetic elastomer manufacturers increase consumption of sugar cane alcohol and reduce our dependence on fossil fuels.
Rubber products made from more eco-friendly polymers have the same properties as those made using fossil fuels.
Vulcanisation as the name implies is the process of application of heat to effect a three dimensional cross linked network. This produces a thermoset part that can be put under stress and strain to a degree without being permanently deformed. Vulcanisation can use many different chemicals and processes. It is a one way non-reversible reaction.
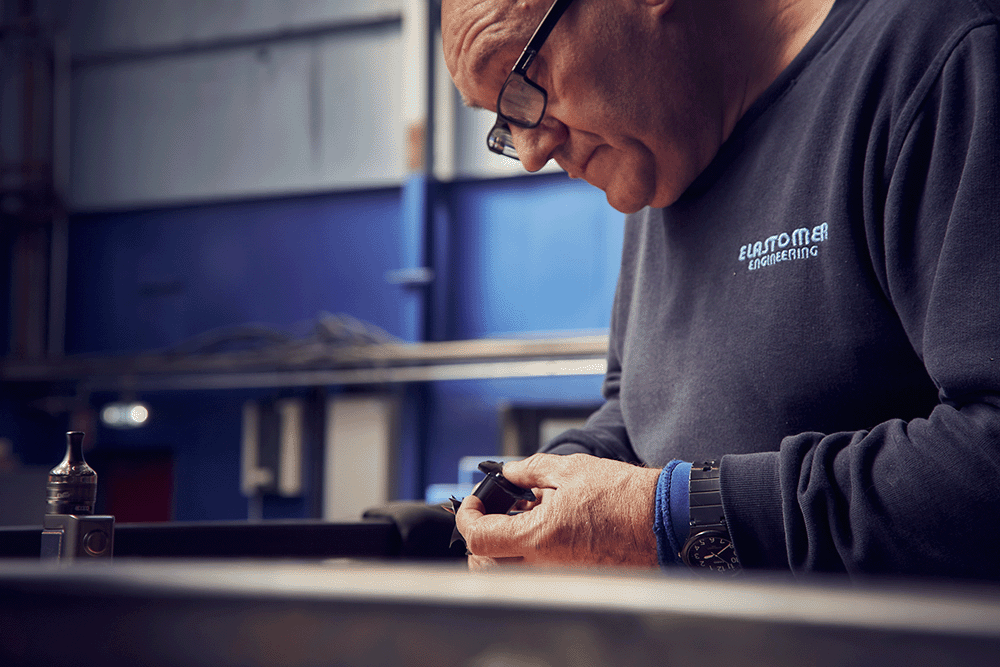
Any questions? Get in touch
Since 1895 DLR has been combining expansive knowledge of materials, their properties, and processing techniques to develop bespoke mouldings and fabrications for many industry sectors. Our core services include moulding rubber, rubber sheeting, Petroseals, and cast polyurethane products. If you have any questions about our products, our process or the materials we use get in touch today!