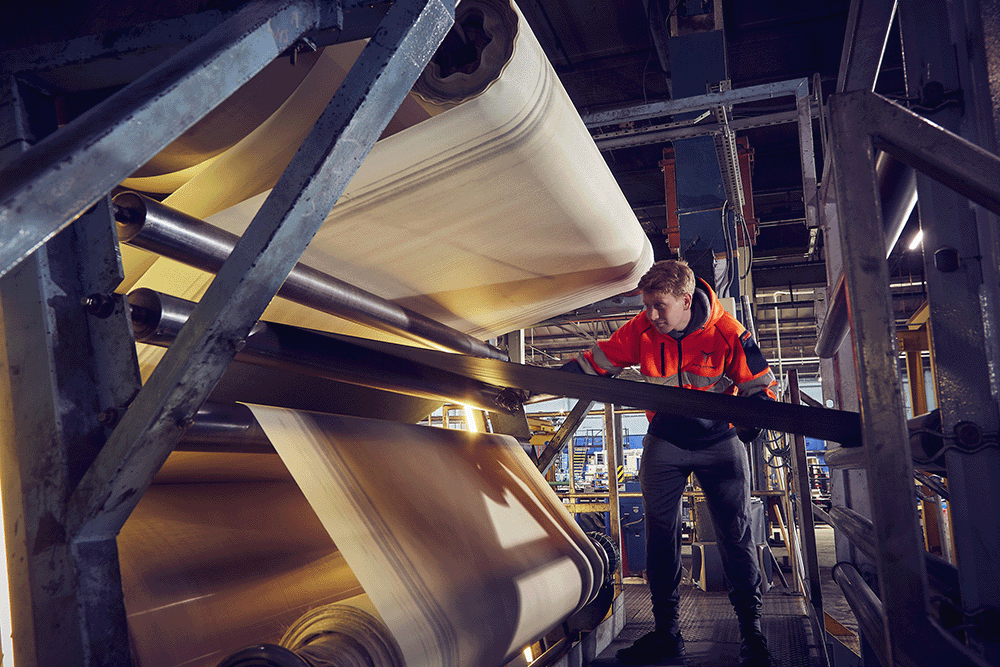
Manufacturer of Bespoke Rubber Sheeting
DLR specialises in providing uncured sheeting in various forms to be fabricated and cured by the client or DLR. Most rubber sheeting is supplied in a cured or vulcanised form, making our rubber sheeting versatile and adaptable. Application-specific materials are chosen, calendared and provided on a roll for subsequent fabrication by the client. In both cases, cured and uncured, woven or knitted textiles may be inserted to produce the desired properties for parts such as diaphragms, stamped gaskets and conveyor belts, to name a few applications.
Rubber sheeting supports applications in many industry sectors. Sheet rubber requires excellent protection properties to work effectively within hazardous environments where exposure to chemicals, weathering and abrasion are commonplace. Due to its flexibility and elasticity at high and sub-zero temperatures, rubber sheeting is typically used as horsebox matting, pond lining, roof covering, fire retardant, and as a gas & chemical barrier in food and medical applications.
DLR have a comprehensive calendaring & rotocuring facility that can produce both vulcanised and unvulcanised sheeting in a range of widths, thicknesses and materials. Our sheeting has been developed for applications in a number of different industry sectors and specialised products, including:
- Calendared Sheet
- Rota cured Sheet
- WRAS EPDM
- Fabric Reinforced Sheeting
- Petro Chemical Seals
- Specialist Fire Retardant Sheeting
- Food Contact Sheeting
- Aqua tape
- Abrasive/Chemical Resistance
- Antistatic / Conductivity
- Vibration / Shock Resistance
Material knowledge is where DLR stands out when it comes to rubber sheeting. Our engineers have the ability to determine the most appropriate materials for your specific application and service conditions. Whether it is antistatic properties required for safe use in potentially explosive environments or pond lining that requires the material to pose no harm to aquatic life, DLR will continuously develop the best solution.

Industries We Supply
Rubber sheeting finds its way into many applications, most of which we all use without realising it. Pond liners, roofing sheeting, sound deadening barriers, washers, and gaskets are all everyday examples illustrating the hidden uses of rubber sheeting.
- Automotive
- Building & Construction
- Industrial Goods
- Aerospace
- Rail
- Food and Water Industry
- Oil and Gas
- Chemical Industry
- Pharmaceutical & Biomedical
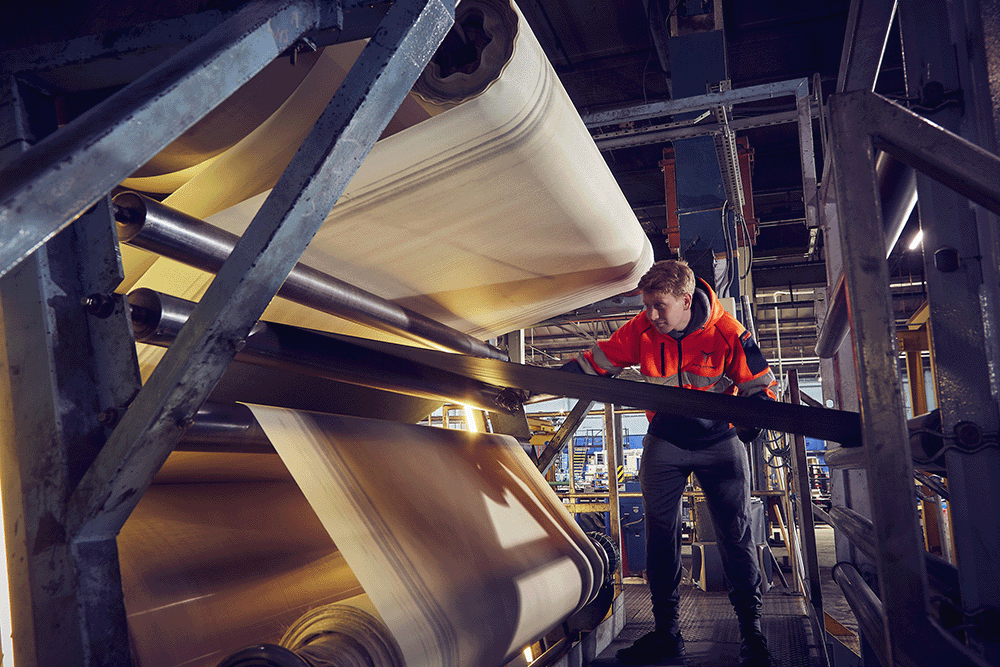
Why Choose DLR Elastomer For Your Bespoke Rubber Sheeting?
DLR Elastomer has been helping our clients with their rubber product requirements since 1895. Our history and our expertise show in our high standards, which we are proud to say are compliant with ISO14001 and ISO9001 standards. All our products are researched, designed, tested and manufactured here in the UK at our Leyland site, and we are proud to comply with the Made In Britain code of conduct.
All our custom rubber medical-grade components are manufactured in-house. Our strict quality control protocols and attention to detail ensure that each client receives a premium product for their particular need. The team here at DLR Elastomer are ready and waiting to speak to you about your requirements, so get in touch today.
Any questions? Get in touch
DLR Elastomer can help with off-the-shelf or predesigned rubber and polymer products, but we are also custom specialists. If you are looking to design and develop a brand-new product, then we have the team to help make this a reality. We are here from the design phase to the manufacture. We have over 125 years of experience behind us, meaning we know what we are doing and have worked with every type of rubber or polymer available today, from natural rubbers to complex polymers – we can handle it all.
If you have any questions or want to know more about our company or the industries we work with, complete the form below, and we will be in touch.
Rubber Sheeting FAQ
Rubber sheeting is produced by calendering rubber compounds to a specified thickness.
The calendering process can take place using any variety of calendar or roller die extruder. The rubber sheet is wrapped in a suitable liner to protect it from sticking to itself and/or provide support during curing.
Curing can be done continuously on a rotocure or press and in batches in an autoclave.
Note that sheeting can be made with fabric reinforcement. The fabric provides strength to the rubber part. The fabric is chosen depending on the application. Woven, non-woven and knitted can be used as can nylons, polyesters, glass, metal and polyaramid.
Rubber sheeting can be used cured or uncured. Uncured can be used for roofing where the uncured rubber facilitates the bonding of the sheets. The sheet cures over time on the roof. Uncured rubber sheeting is used in damp proofing for houses.
Reinforced and unreinforced cured rubber sheeting can be used for gaskets, where parts are stamped out of the sheet. Rubber sheeting is used as flooring and, when compounded and fabricated correctly, can be used for orthopaedic anti-fatigue mats for humans and animals (cow and horsebox mats).
Rubber sheeting is used for protecting floors and machinery from spills in industrial environments. Pond liners and roofing are two of the biggest uses of rubber sheets as both utilise rubber’s water retention properties. When compounded correctly, rubber sheeting can be used for sound deadening in the automotive industry. Another use of rubber sheeting is diaphragms which can be reinforced to provide long life.
In short, the answer is yes.
A few techniques can be employed with rubber sheeting, although the ideas are very much the same as rubber to metal bonded parts.
Coating rubber onto metals can be done by using solutions of rubber in suitable media, normally solvents. They can be dipped and then vulcanised. Depending on the amount of rubber required, over-moulding may offer a better solution.
Rubber can provide a heat or chemical barrier to metal parts. As rubber insulates, it offers a warmer surface to hold on to and provide grip or friction for leverage, for example, power tool grips and screwdrivers.
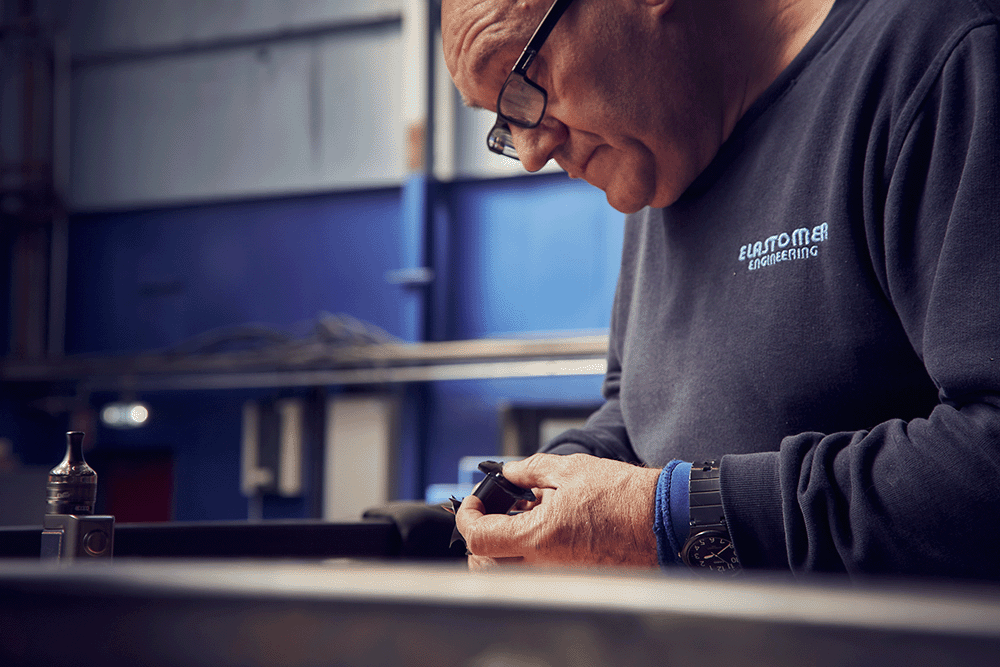
Any questions? Get in touch
Since 1895 DLR has been combining expansive knowledge of materials, their properties, and processing techniques to develop bespoke mouldings and fabrications for many industry sectors. Our core services include moulding rubber, rubber sheeting, Petroseals, and cast polyurethane products. If you have any questions about our products, our process or the materials we use get in touch today!