
Custom-Designed Rubber Bellows & Expansion Joints
Bellows and expansion joints serve a range of diverse roles, such as reducing noise and vibration, protecting mechanical elements from dust, resisting the potential impact of shifting temperatures and pressure, and curbing the effects of misalignment. Here at DLR Elastomer, we have been helping our customers with their custom rubber requirements for over 125 years. We combine our decades of experience and knowledge of rubber products with our design and manufacturing capabilities to produce some of the highest-quality rubber bellows and expansion joints that our industry partners need. DLR Elastomer can help with rubber bellows, rubber expansion joints, flexibles and compensators for various uses for a wide range of industry partners, including the automotive, chemical, food and oil and gas industries.

Leading Materials For Manufacture
We can manufacture your bellow and expansion joint product requirements using leading materials from the rubber industry, including:
- Nitrile (NBR)
- Hydrogenated Nitrile (HNBR)
- Ethylene Propylene (EPDM)
- Silicone (VMQ)
- Polytetrafluoroethylene (PTFE)
- Fluorosilicone (FVMQ)
- Perfluoroelastomer (FFKM)
Why Choose DLR Elastomer?

Bellows & Expansion Joints FAQs
- Rubber Bellow: A rubber bellow, also known as a rubber expansion joint, is a flexible connector fabricated from natural or synthetic elastomers and fabrics with metallic reinforcements designed to provide stress relief in piping systems due to thermal and mechanical vibration and/or movements. They are flexible, which allows for compression, extension, and angular movement. They are often used in systems where there are large amounts of vibration, such as pumps or compressors. Additionally, they can also be used in systems where there is thermal expansion, as the rubber can expand and contract with temperature changes.
- Expansion Joint: An expansion joint is a general term that refers to any device that allows for movement due to thermal expansion and mechanical vibration in a piping or ducting system. This can include rubber bellows, but it can also include metal bellows, and other types of expansion joints made from various materials like fabric, PTFE (Teflon), etc. There are also different types of expansion joints designed for different types of movement, including axial, lateral, and angular expansion joints. They are typically used in large-scale industrial applications, such as power plants or chemical processing plants, where there is a need to accommodate large amounts of thermal expansion and contraction.
- Natural Rubber (NR): This is used for its high elasticity, excellent tensile strength, and resistance to abrasion and fatigue. However, it’s not very resistant to oils and certain types of chemicals.
- Neoprene (CR): Neoprene is a general-purpose elastomer with good mechanical properties, and it’s resistant to weathering, ozone, and ageing. It’s also resistant to many chemicals and oils and can operate at a wide range of temperatures.
- Nitrile (NBR): Nitrile rubber is highly resistant to oils and fuels, making it ideal for oil and gas applications. It also has good mechanical properties and can operate at various temperatures.
- Ethylene Propylene Diene Monomer (EPDM): EPDM has excellent resistance to ozone, weathering, and ageing. It also has good resistance to many types of chemicals, but it’s not suitable for use with oils and fuels.
- Styrene-Butadiene Rubber (SBR): SBR is a general-purpose rubber with similar properties to natural rubber. It has good abrasion resistance and excellent impact strength.
- Silicone (VMQ): Silicone rubber can operate at high and low temperatures. It’s also resistant to weathering, ageing, and sunlight, but it’s unsuitable for oils and fuels.
- Fluorocarbon (FKM, also known as Viton): Viton is resistant to a wide range of chemicals and oils and can operate at high temperatures. However, it’s not as flexible as some other types of rubber, and it’s more expensive.
It’s crucial to carefully consider the application’s specific requirements when selecting the material for the rubber below, as each type has its strengths and weaknesses.
Any questions? Get in touch
DLR Elastomer can help with off-the-shelf or predesigned rubber and polymer products, but we are also custom specialists. If you are looking to design and develop a brand-new product, then we have the team to help make this a reality. We are here all the way from the design phase to the manufacture. We have over 125 years of experience behind us, meaning we know what we are doing and have worked with every type of rubber or polymer available today, from natural rubbers to complex polymers – we can handle it all.
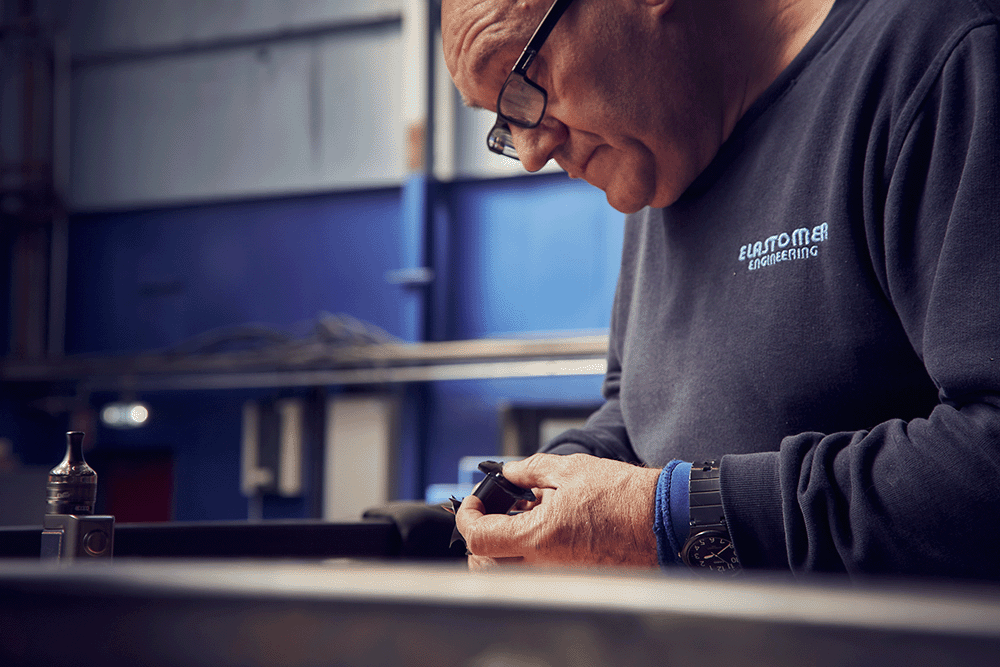
Any questions? Get in touch
Since 1895 DLR has been combining expansive knowledge of materials, their properties, and processing techniques to develop bespoke mouldings and fabrications for many industry sectors. Our core services include moulding rubber, rubber sheeting, Petroseals, and cast polyurethane products. If you have any questions about our products, our process or the materials we use get in touch today!