Looking for more detailed information on the different types of rubbers and polymers we work with? Then check out our material guides where you can find FAQ’s and more guides like this one detailing all you need to know. If you are looking for rubber or polymer products get in touch with DLR Elastomer today via our contact page or via LinkedIn and we can chat over your requirements.
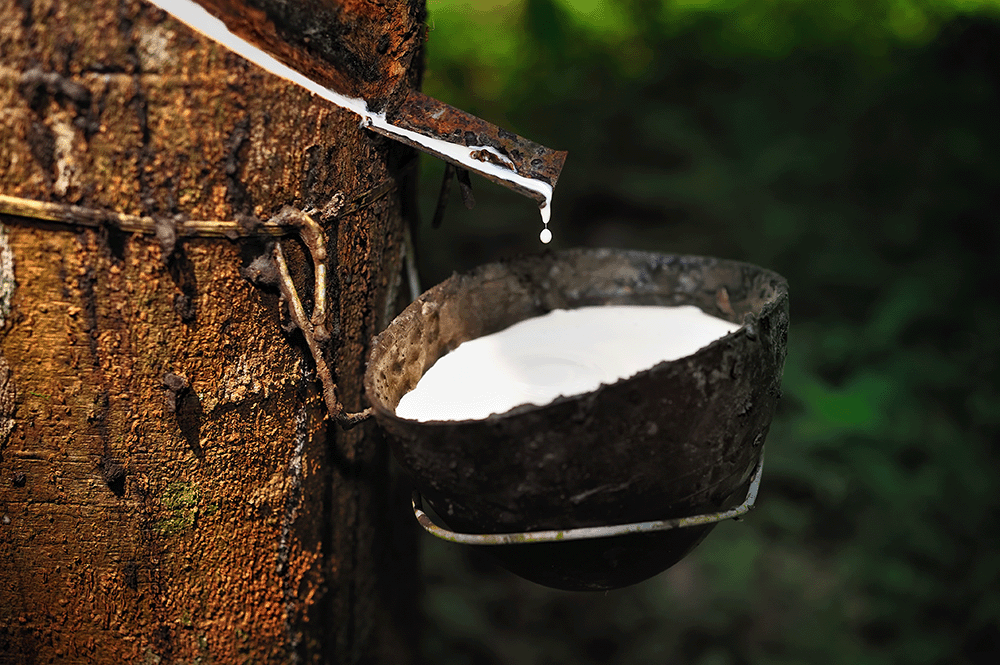
What Raw Materials Are Used to Make Rubber?
What Raw Materials Are Used to Make Rubber?
Rubber is everywhere. It is a ubiquitous material that consumers and manufacturers alike rely on to go about their daily lives and operations. But have you ever wondered what raw materials are used to make rubber? Wonder no more because DLR Elastomer Engineering is here to give you our in-depth guide to everything that goes into the manufacture of rubber.
There are in the region of 10,000 rubber ingredients available to us as expert manufacturers of polymer products. There are around 20 polymers that we can choose from, with each one having more than one supplier. Not to mention subtle and significant differences in their properties. When it comes to developing custom rubber mouldings, we categorise our rubber compounding ingredients according to their purpose.

Polymers
- Natural Rubber (NR), Styrene Butadiene Rubber (SBR), Butyl (IIR), Halogenated Butyl (XIIR), Isoprene (IR), Butadiene (BR) – These are polymers used primarily in tyres.
- Neoprene (CR), Nitrile (NBR), PVC/NBR, EPDM – These are general-purpose rubbers that provide fuel, oil, chemical, water, UV, ozone and weather resistance. They also deliver better heat resistance than NR, IR and SBR.
- EVA, Polyurethane, XNBR, Hypalon (CSM), Epichlorohydrin (ECO), Ethylene Acrylic (AEM/Vamac) – These are special polymers, used at higher temperatures than others and have their own individual characteristic properties. For example, AEM is used in fire retardant applications. It is halogen free and emits non-toxic smoke.
- Hydrogenated Nitrile (HNBR), Acrylic (AEM), Silicone (VMQ), Fluorosilicone (FVMQ), Aflas (TFE/P), Fluoroelastomers (FKM), Perfluoroelastomers (FFKM) – These polymers are used in demanding and aggressive environments. These include oil and gas, deep sea and chemical installations requiring the highest levels of heat and chemical resistance.
Note that the above polymers are made in multi-million pound polymerisation plants where monomers such as styrene and butadiene are reacted under pressure to produce rubber (Styrene Butadiene Rubber or SBR in this example). Every polymer has its own monomers and polymerisation chemistry. Each is made with a specific molecular weight (or Mooney Viscosity), balancing the physical properties and the processing required.
Polymers on their own, without the addition of other ingredients, find little use. The notable exception is oil modification. Polymers can be added to oil in order to maintain a constant viscosity with increasing temperatures, with a prime example of this being motor oil. Most polymers are used in the cured or vulcanised state to obtain the optimum physical properties required for the application and service life.
Fillers
Fillers are added to reinforce the polymer for improved physical properties, better processing and bulking out the polymer for cost-effectiveness. The vast majority of rubber applications are black. This is due to the use of a reinforcing, organic filler called carbon black. They are available in many grades that each impart their own unique set of properties to the polymer and subsequently the resulting compound and final product.
Many non-reinforcing fillers are used in polymers to make non-black rubber goods for industries, such as shoe soles, food, medical and pharmaceutical products. The only reinforcing non-black filler is silica. Fillers in this category are inorganic, such as whiting (calcium carbonate), talc (magnesium silicate), clay and silica (silicon dioxide) to name but a few. Specialist fillers for flame retardancy and other properties are also available.
Plasticisers
Polymers need the addition of some fillers to make them process better. Fillers tend to increase the hardness and produce stiff compounds and eventually harder parts. To counterbalance this effect, plasticisers or oils are used.
The most common types include:
- Mineral Oils
- Paraffinic, Naphthenic, Aromatic
These are widely used and provide good processing rubber compounds. They can be used in commodity rubbers within limits. For oil resistant and specialist rubbers, synthetic oils are used. These tend to be of the ester type and are used for their application-specific properties. For instance, providing flexibility at sub-zero temperatures, flame retardancy or antistatic properties.

Antidegradants
In order to develop rubber products that provide a good degree of protection within their application environment, various additives can be added. Polymer degradation can take place due to attack from a combination of any number of the following:
- Chemical > Oxygen, Ozone
- Hydrolytic > Water
- Thermal > Heat, Pyrolysis
- Photolytic > UV
- Biological
- Radiation
- Mechanical
Various ingredients provide the rubber product with a level of protection in service. All materials are subject to attack from any of the above. For example, photons of light, oxygen or ozone radicals react with unsaturation in the polymer backbone and start the degradation cycle. The additives used to counter the degradation absorb the free radicals, stopping the main polymer chain from being attacked and any further degradation from taking place.
The chemicals that we use range from microcrystalline waxes for ozone protection to phenol-based antioxidant and UV protectors. Para-phenylenediamines are commonly used, although these are staining. Most antidegradant systems use a combination of chemicals.
Blowing Agents, Pigments, Bonding Agents
Certain additives are used to provide specific properties to rubber compounds. Blue is the colour generally preferred in the food industry. Food manufacturers also prefer the rubber to be metal detectable. Many pigments are available, which are both organic and inorganic. Red oxide and yellow ochre are examples of inorganic materials, while an example of organic materials are azo dyes.
In order to stick rubber to metal or other substrates, bonding agents may be needed in the rubber, as well as appropriate treatment of the substrate. Some applications – such as car door profiles – require blown, foam or sponge rubber. The holes or cells in the rubber are created by adding materials that release nitrogen during heating. The curing reaction traps the gases as the rubber expands.
Curing Agents
Having added many ingredients to the rubber, we now have a compound that has the consistency of plasticine. This material has to be cured under heat and pressure for it to take on a shape that can be retained when deformed. Sulphur can be added to effect crosslinks and provide a three-dimensional cross-linked network. As the reaction with sulphur is slow, various types of accelerators are added to speed up or accelerate the reaction.
This process of using accelerators enables products to be made more efficiently. However, care must be taken when selecting these additives. This is because they influence many aspects of production (process safety, shelf life) and service life (crosslink density, dynamic mechanical properties).
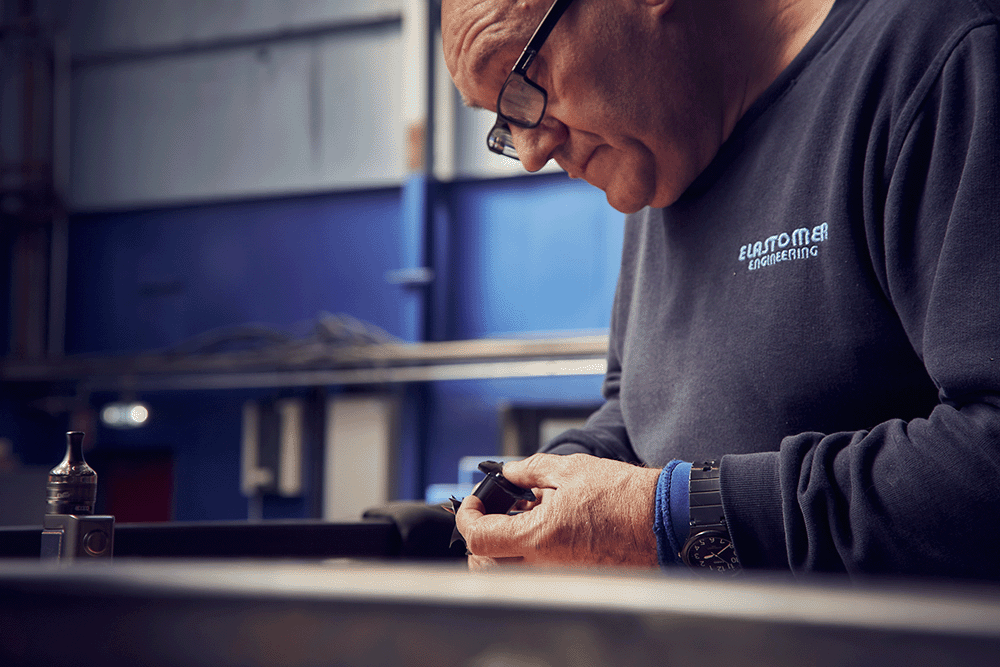
Any questions? Get in touch
Since 1895 DLR has been combining expansive knowledge of materials, their properties, and processing techniques to develop bespoke mouldings and fabrications for many industry sectors. Our core services include moulding rubber, rubber sheeting, Petroseals, and cast polyurethane products. If you have any questions about our products, our process or the materials we use get in touch today!